Green Energy Solutions and Cogeneration
Cogeneration is an easy way for you, the customer, to greatly cut your fuel bill
and cut your carbon footprint in half by making better use of the source fuel.
This paper lays out some bricks of understanding so you can build your own cogeneration
cycle or feel free to contact Green Energy Engineering, Inc. and we can custom design
a cogeneration cycle for your process.
What is Cogeneration?
- Cogeneration is simply the dual production of useful thermal energy and electricity from one fuel source
- Cogeneration is also called combined heat and power
/>
- Cogeneration can also be distributed generation
- Cogeneration is a thermodynamic term and not the name of a company, as some mistakenly
think
- Cogeneration has been around for over 100 years and originally got started in pulp
mills and chemical plants where steam and electricity were produced and used
- Cogeneration can produce electricity, shaft horsepower, steam, hot water, hot air,
air conditioning, desiccant drying and other useful energy based process
- Cogeneration can allow you to consume energy at 60%, 70%, 80% or 90% efficiency
rather than the typical 20% to 30 % efficiency cycle
- Cogeneration can cut your carbon footprint in half or more
- Cogeneration can greatly reduce your purchased fuel cost
Energy and Quality:
You can do more useful things with a bottle of propane then you can with a hot water
solar panel. While both represent energy, they also have a quality component. The
hot water solar panel can be used to make hot water, provide space heating in the
winter, or if supplemented with another booster energy source, produce air conditioning.
The bottle of propane on the other hand can do all those things and heat a bar-b-que
grill or drive a small engine. The engine in turn can provide shaft horsepower for
pumping or spinning an electrical generator.
Quality and Temperature:
The quality of energy can be related to temperature. The higher the temperature
the more things it can do. The hot water solar panel which might reach 130°F cannot
be used to operate a jet engine. However, high grade kerosene, burning at 2,000°F,
can be used in a jet engine. Other fuels like oil, natural gas, coal, and wood burning
at temperatures in excess of 1,000°F, can be used to operate boilers or engines
that in turn can produce electricity or shaft horsepower.
Carnot Cycle:
In 1824, the French physicist Nicolas Leonard Sadi Carnot wrote a paper called,
“Reflections on the Motive Power of Fire,” in which he provided a theoretical framework
for describing heat engines such as the gasoline engines, diesel engines, or jet
engines. The theory states that the highest theoretical efficiency that can be achieved
by a heat engine (like a gasoline engine) can be calculated by “mathematically operating”
a Carnot heat engine between a hot source sink and a cold reject sink. While the
Carnot heat engine is simply a mathematical concept, it clearly represents the ceiling
of efficiency. Real obstacles such as incomplete combustion, heat loss, and friction
will result in an even lower efficiency. The concept of the Carnot cycle is as follows:
The efficiency of this heat engine is mathematically described as follows;
η = 1 – Tc / Th
Where:
η = efficiency in percent
Tc = Temperature of the cold reject sink in °Rankin
Th = Temperature of the hot source sink in °Rankin
Note – 0.0°F = 460 °Rankin or °R = °F + 460
Assume that there is a heat engine operating between a hot source sink of 140°F
to 1000°F in several 200°F steps. Also assume that the cold reject sink is operating
at a constant 120°F temperature. The table below has several temperature cases laid
out left to right. The top row is temperature in °F , which is how most of us think.
The second row in simple °R , which is °F plus 460. The cold reject sink temperate
has the same double listing for ease of understanding and the center row indicates
the heat engine efficiency. The efficiency at each point would be a follows;
Notice that the heat engine efficiency increases as the hot source sink temperature
increases. This is why researchers and engineers have been working on increasing
the firing temperature of boilers, engines and especially jet engines. Jet engine
turbine blade metallurgy, coatings, and cooling have progressed tremendously in
the past 20 years and more is on the way.
The fallacy of the above example is the exhaust or cold reject sink temperature.
It is far too cold compared to real engines. The following table shows a more realistic
estimate of typical operating temperatures for several types of engines.
An internal combustion gasoline engine might have a burning temperature of 700°F
and an exhaust temperature of 400 while a diesel engine might have an ignition temperature
of 900°F and the same exhaust temperature of 400°F. A jet engine might have a firing
temperature of 1700°F and an exhaust temperature of 1000°F. These types of engines
and the temperature results in low overall engine efficiency compared to cogeneration.
Cogeneration Cycle:
A cogeneration cycle is able to make use of more of the available source energy
by using the reject exhaust temperature of one thermodynamic cycle as the input
to another thermodynamic cycle such as the following;
Assume that the hot source sink shown above is natural gas burning at 1,700°F in
a combustion turbine generator and that the smoke stack exhaust temperature is 1,000°F.
From the previous table we know that this would yield an engine efficiency of 32%.
Now assume that this high temperature exhaust is now used as the input to a heat
recovery steam generator producing 150 psig process steam and that the smoke stack
exhaust temperature is 350°F. According to the following table, this second process
has an efficiency of 45% and the overall cogeneration efficiency is 77% (32% + 45%)
which means that more of the source energy (in this case natural gas) has been used.
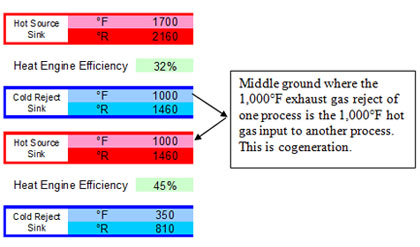
Hot Water:
Domestic hot water or hot water heat in the winter can be produced from an electric
hot water heater, a natural gas heater, or a solar panel. The cheapest source is
the solar panel. Since the water only needs to be 100°F to 140°F then it makes financial
sense to use the solar panel and keep the high quality fuels for a higher better
use. We burn gasoline in a small engine and the exhaust is hot. The engine might
be 20% efficient. If the hot exhaust is captured in a heat exchanger, it can heat
air or water for other uses. This is simply a small example of a cogeneration cycle
that might now be 40% efficient because of the captured and used waste heat. Residential
air conditioners here in Florida have been retrofitted with lunch box-sized heat
exchangers for over twenty years. The hot Freon gas from the compressor heats domestic
hot water first and then flows to the condenser coil for more heat rejection before
flowing inside to the evaporator coil. This is also cogeneration.
Process First:
The secret to a cost effective cogeneration cycle is to understand the process first.
What is the process? Where is energy used? Are there other ways to do “it” with
a different energy? What is the true thermal load? What is the electric load? Can
any of the electric load be changed to another source like steam turbines or small
combustion turbines? Have you done an energy audit? Have you analyzed the heat exchangers
under a Pinch technology framework to understand the heat flows and temperatures? These
are just a few of the many questions that need to be answered before a cogeneration
cycle can be customized and optimized for both the process requirements and the
project rate of return.
Cogeneration Cycles:
The following is just a short list of the types of cogeneration cycles that Green
Energy Engineering, Inc. has developed over the years.
-
Wood fired steam boiler driving a steam turbine generator with 150 psig exhaust
for process steam.
- Natural gas fired combustion turbine generator with hot exhaust
gas routed to paper machine hot air drying system.
- Oil fired steam boiler driving
a steam turbine generator with 150 psig extraction and 10 psig back pressure.
-
Natural gas fired combustion turbine generator with hot exhaust going to a heat
recovery steam generator for process needs.
- Oil fired diesel engine generator
with both jacket cooling water and hot exhaust gas going to a heat recovery unit
to provide process hot water.
- Light oil fired combustion turbine driving an oil
transport pump with hot exhaust used to heat the oil for lower viscosity for 90
mile oil transport pipe line.
- Natural gas fired combustion turbine generator with
hot exhaust used to produce hot water and then produced cold water in an absorption
chiller.
- Natural gas fired combustion turbine generator with hot exhaust flowing
into an oil fired boiler with conventional steam turbine generator. Also known as
hot wind box.
- Bark fired boiler with steam flowing to a multi pressure extraction
steam turbine generator.
- Sulfur fired boilers providing steam to steam turbine
generator with extraction for evaporator use.
Hire a real professional engineer:
The purpose of this cogeneration article is to provide an overview and introduction
of the subject to the novice reader. This is a short paper with simple examples
and the reader is encouraged to retain the services of an experienced licensed professional
engineer, who has a track record of technical and financial success with cogeneration.
The concepts presented here are simply some of the rain drops that eventually make
a river. Hopefully this process perspective of the thermal cycles involved leaves
the reader with the idea that there is no “one size fits all” solution. History
has a debris field of those who only focused on the electrical side and ignored
the process side. Some call this electric only focus a “PURPA Machine” (Public Utility
Regulatory Policies Act) because the thermal load was questionable. The economics
were questionable and some of those projects are no longer in operation. When properly
developed, a process based cogeneration cycle can save fuel, save money, and save
the Earth.